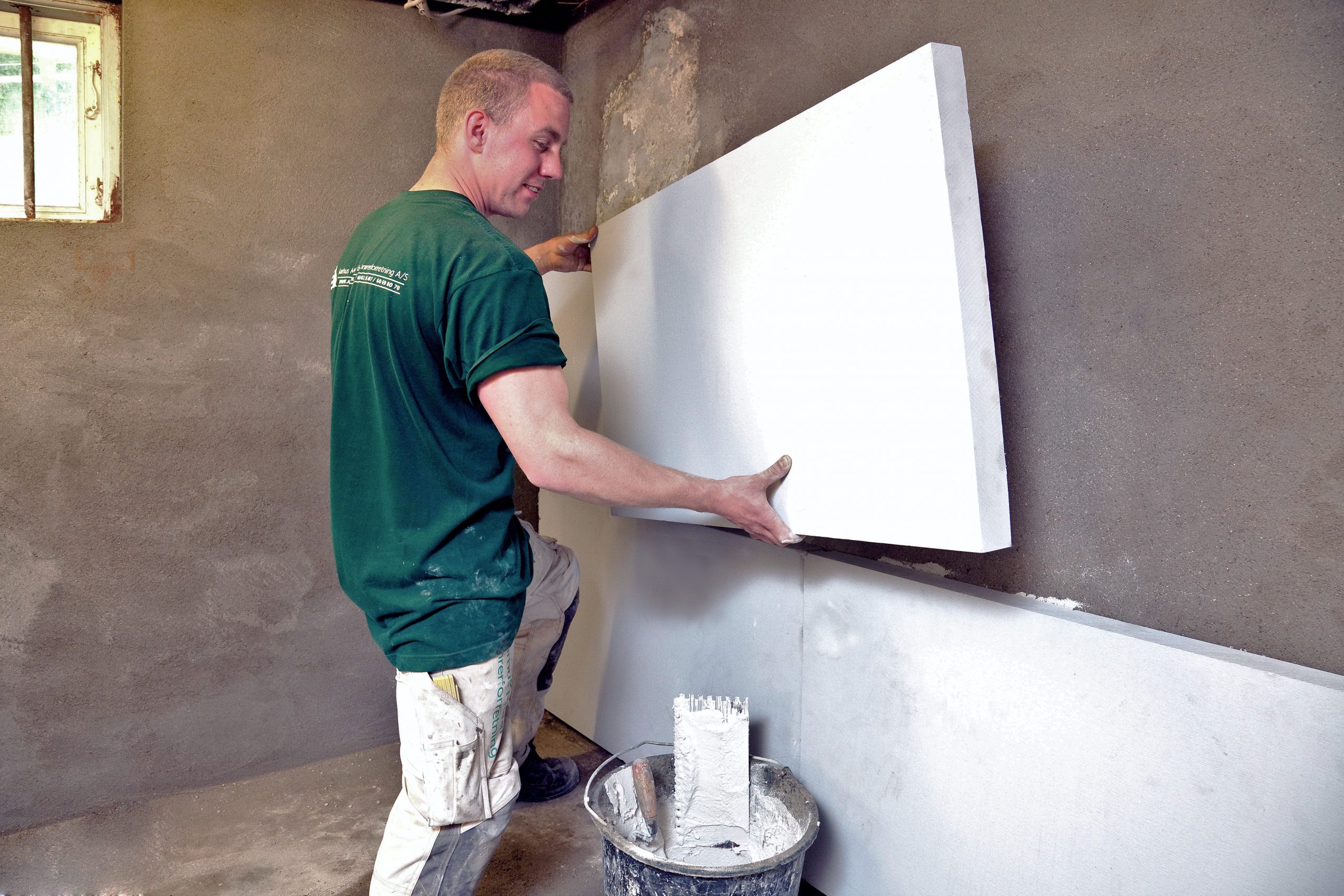
Liquid applied airtight membranes first arrived in the UK around 5 years ago. The idea that an airtight membrane could be spray or brush applied was ground-breaking despite the use of similar means of application for protective coatings and waterproofing. Blowerproof was first introduced to the UK by Ecomerchant in early 2016. The product became BBA certified (the first to do so) in 2017 and was quickly picked up by the Passive House sector.
Over the past two years, liquid applied membranes have seen exceptional growth as the demand for airtight buildings increased. The ultimate application came in spring 2019 when the Imperial War Museum archive used Blowerproof to create the most airtight building in the UK (ACH 0.03) for storing its priceless archive of documents.
For the refurb sector, the use of liquid applied membranes is a game-changer. The water-based VOC free liquid can be applied to almost any surface even in the trickiest and most demanding applications it creates a permanent flexible layer which allows airtightness to be delivered where previously achieving high levels were nigh on impossible.
Wood fibre flexible batts and rigid carrier boards. Insulation is a key component of most retrofit projects and the increase in wood fibre use over the past few years has been steady – but the take up this year has been exceptional. Wood fibre is a versatile product, which offers desirable performance characteristics for new build and renovations. Being vapour permeable it helps buffer moisture, its density (up to 250Kg/m3) protects against overheating and its natural makeup alleviates concerns over synthetic ingredients, off gassing and poor indoor air quality. The flexible batts are popular for installation between studs and the dense rigid boards for carrying render or plaster either internally or externally on timber frames or direct to masonry or brick.
Calcium silicate boards; the elimination of mould and subsequent reduction in health issues has driven sales of SkamoWall Board. The calcium silicate board is part of a system which includes adhesive, primer and plaster that combine to create a buffer to manage moisture, improve insulation and eliminate mould. The board’s inert chemical structure renders it incapable of supporting mould growth. The improved insulation and breathability of the system allow ventilation to harmlessly remove moisture from the building. The plastered board acts as a vapour control layer whilst remaining breathable. The SkamoWall Board has been a favourite of landlords and owners of older buildings with solid walls where persistent problems often cause unwelcome maintenance costs and tenant complaints.
Education is a key specification tool
The use of these products is exclusively a matter of personal choice so why are they so popular? There are several answers but largely this is to do with how educated the buyer is about building features that are desired but not mandatory within building regulations. For non-developer new build this demand is clear and growing, driven by a client who include improved building performance and occupant health within the brief. For retrofit one reason may be the limits on design imposed where a significant uplift in performance can be achieved through upgrading the building fabric where options such as orientation, outward changes to shape or ‘look’ and modifying the footprint are not possible so forcing a more open approach to problem-solving.
The UK construction sector knows that there are widespread problems with carbon, energy, moisture, ventilation and health in our housing stock. But they persist in partial and piecemeal solutions, apparently oblivious to the interactions between these problems and the need for a holistic approach. A change of attitude and major upskilling of the workforce, especially in refurbishment projects, is required to deliver effective solutions to the enormous backlog of remedial works required to deliver the healthy, comfortable and affordable homes that are essential if the UK is to meet its carbon targets.
Health matters
Since lockdown in March increased awareness of the way our buildings actually perform has been consequence of many of us spending more time at home, we have experienced how our buildings perform at times we would usually be absent i.e. during the day when we would otherwise have been at work. Increased focus on our health has broadened the interest and understanding of how building design and fabric can have a direct effect on our wellbeing, at the least this is shown as a precautionary approach to avoid known producers of toxins such as VOC’s or formaldehyde (prompted by the lockdown boom in home decorating and refurbishment) or on insufficient insulation or ventilation; at best our focus has shifted to including building health and indoor air quality (not mandated through building regulations) as part of what we need to demand from our homes and workplaces.
No carrot but no stick either!
On the subject of what is mandated and what is not 2020 is ending with a familiar scenario of promised changes and little real regulatory progress. The government has finally published plans for a new version of Approved Document L (for energy efficiency), a new F (for ventilation), and confirmed a new regulatory standard for managing summer overheating is on the cards. This consultation phase is still in progress.
These documents currently apply to new-build homes in England, but we can expect further publications to pick up on Welsh standards, non-domestic development and existing buildings. Notice that retrofit is still not a priority despite estimates that around 80% of the homes we will be occupying in 2050 already exist.
The UK GBBC report ‘Net Zero Carbon Buildings: A Framework Definition’ which was launched at the Houses of Parliament in April 2019 provides a framework on how to achieve net-zero carbon buildings in both construction and operation (in-use energy consumption), whilst beginning to provide direction for addressing whole life carbon in the industry. Again this projects well into the future with targets set for 2030 for new build but not until 2050 for existing buildings.
The much-vaunted PAS2035 (linked to the requirement to implement PAS2030) launched last summer is still not a mandatory requirement except for certain types of funded retrofit project, this excellent standard is advised rather than imposed so, therefore, is unable to deliver the intended improvements to existing homes at scale for the moment. Mandatory inclusion of PAS 2035 is currently scheduled from July 2021 for ECO (Energy Company Obligation) projects only.
We are yet to feel the full effects of the Hackitt review and to cap the year off nicely we still have an unresolved Brexit to muddy the waters and prolong inaction.
If we are to ‘build back better’ the connection between buildings that are low in embodied carbon, low energy users, that manage moisture through material choice and design, are healthy and nontoxic to the occupants and durable, can be summed up by a requirement to simply build healthier buildings an ambition that is sadly lacking from almost all the current providers.
The housing crisis has not gone away
We still have a crisis within the housing sector to deal with and a lot of this is tied in with energy efficiency and energy use. The nature of the problem is neatly encapsulated by Richard Tibenham director of Greenlite Energy Assessors and associate lecturer of building physics at the University of Lincoln. Tibenham refers to The Committee on Climate Change report ‘UK Housing: Fit for the Future?’ which claims that emissions reductions from the UK’s 29m homes have stalled, while energy use in homes increased between 2016 and 2017. It further claims that we will not meet our legally binding targets for emissions reduction under the Paris Agreement without near-complete decarbonisation of the housing stock by 2050.
At present, there is no agreed solution to modify the built environment such that it can operate in a carbon-neutral fashion by 2050. The problem can be made substantially less dire, however, by not adding yet further energy demand at this critical time.
So whether it is carbon reduction in building operation, energy generation, design or materials choice we are facing the absolute need to decarbonise the sector, and this will need to be backed by mandatory regulations.
New build can rapidly become a retrofit problem.
Lord Deben Chair of the UK CCC sums this all up rather neatly saying “there are other influences on housing emissions. For example, there is the fact that the Government still have not raised the standards for new buildings. At the moment, we are building more trouble every year[i]” in essence poor standards for existing buildings just increases the size of the retrofit market. They condemn most of what we are building now to retrofitting in the future a frankly crazy notion when we are already faced with the challenge of upgrading the energy performance of the entire housing stock, it is nonsensical to be continuously making the problem worse by allowing new homes to be built that will also need to be retrofitted, which begs the question why not build better now especially if this is straightforward to achieve. This situation is made worse by the various ways in which the law allows buildings to be built to historic standards[ii] astoundingly Government data shows that 62 per cent of homes that Persimmon built in 2018 were to standards that pre-date the 2013 Building Regulations, as were 52 per cent of Taylor Wimpey’s and 47 per cent of Barratt’s. They are not alone as government data shows that 12 per cent of the new homes built in 2018 were rated EPC C, whilst 7 per cent were rated D or below[iii].
So little remains in terms of positive regulatory drivers for the present. One option is to elect to use a voluntary standard such as The Passivhaus Institute developed ‘EnerPHit Certificate’ (a quality-approved energy retrofit with Passivhaus components). This certificate sets a slightly different standard requirement to the full Passivhaus standard. Each home and building is unique and poses specific problems and solutions to reduce carbon emissions, improve energy efficiency and ultimately achieve greater energy security.
However, EnerPHit does not directly address the issues of moisture and occupant health although it could be argued that they are mitigated by improved fabric and performance. In retrofit, in particular, there does need to be sympathy between the existing structure and the intended use, ensuring that the building functions without the likelihood of creating unforeseen problems that may later degrade the fabric. This requires a holistic approach and the use of a range of materials and resolutions to create a long-lasting energy efficient healthy building.
The use of non-standard materials like the ones highlighted by Ecomerchant does indicate to us that this process is underway and that there are many who will not wait for legislation to catch up. In fact they may well reap extra benefits in the future when others are faced with costly upgrades simply to bring buildings into compliance.
[i] Lord Deben, Chairman, Committee on Climate Change Business, Energy and Industrial Strategy Committee Oral evidence: Energy Efficiency, HC 1730 Tuesday 26 March 2019
[ii] See notes 131-4 Select Committee BEIS Energy efficiency and net zero 12th July 2019 https://publications.parliament.uk/pa/cm201719/cmselect/cmbeis/1730/173009.htm#footnote-047
[iii] Ministry of Housing, Communities and Local Government, Live tables on Energy Performance of Buildings Certificates (2018)