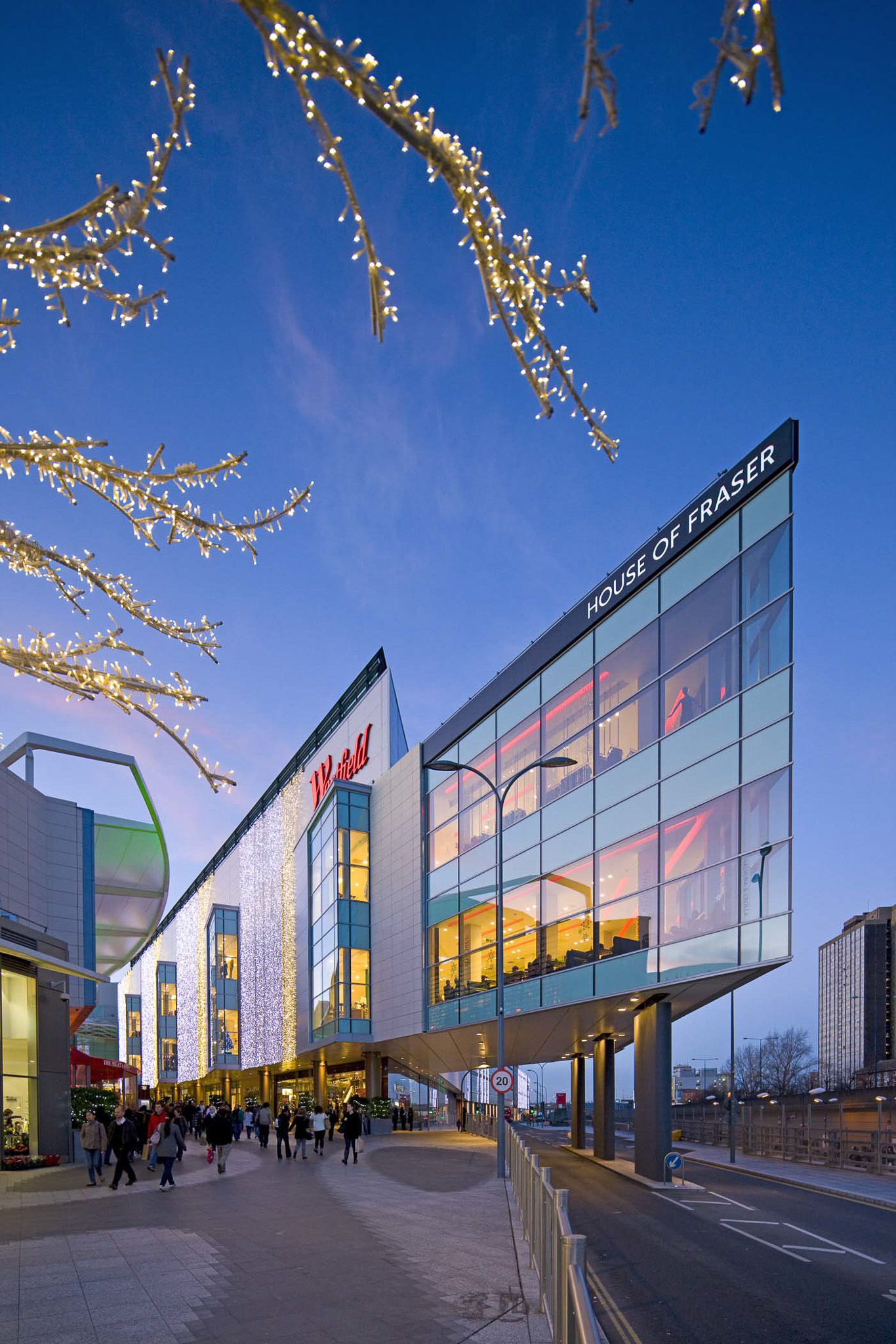
By Chris Mansfield – QUALICOAT Chair
Architectural Aluminium Powder Coating is applied using the well known methodology of spraying electrostatically charged fine polyester based powders onto a product. Coated aluminium products are then heated to an optimum temperature to melt the powder which allows it to flow and chemically cross-link into a sustainable coating. As the product cools the coating sets and the finish is complete. The problem is, like most applied opaque coatings, the finish may look good, but the coating can hide a multitude of problems on the surface of the metal. If contaminants are present, or a pre-treatment process is lacking, a failure of the coating will become evident over time.
Prior to powder coating architectural aluminium, it is crucial that the aluminium surface is subject to a ‘pre-treatment’ process which includes an etch stage to remove contaminants and then a passivation or conversion coating to ‘seal’ the surface of the aluminium which also provides a ‘key’ for the adherence of the coating. These very thin conversion coatings can be formed of a non-chromate or a very thin anodising process.
For an architectural powder coater a pre-treatment plant is a significant investment often costing as much, if not more than the powder coating line itself. Few powder coating lines in the UK have this substantial facility and those that do will claim to powder coat to BS EN 12206-1 or become licensed to powder coat to the more substantial QUALICOAT specification.
Often in an attempt to reduce costs through the supply chain, installers of architectural aluminium products will use powder coaters who often do not possess the correct pre-treatment lines. There is also the possibility that some coaters who do have the correct pre-treatment systems do not have suitable controls in place and the quality of the coatings can vary, even though they can claim to coat to BS EN 12206-1.
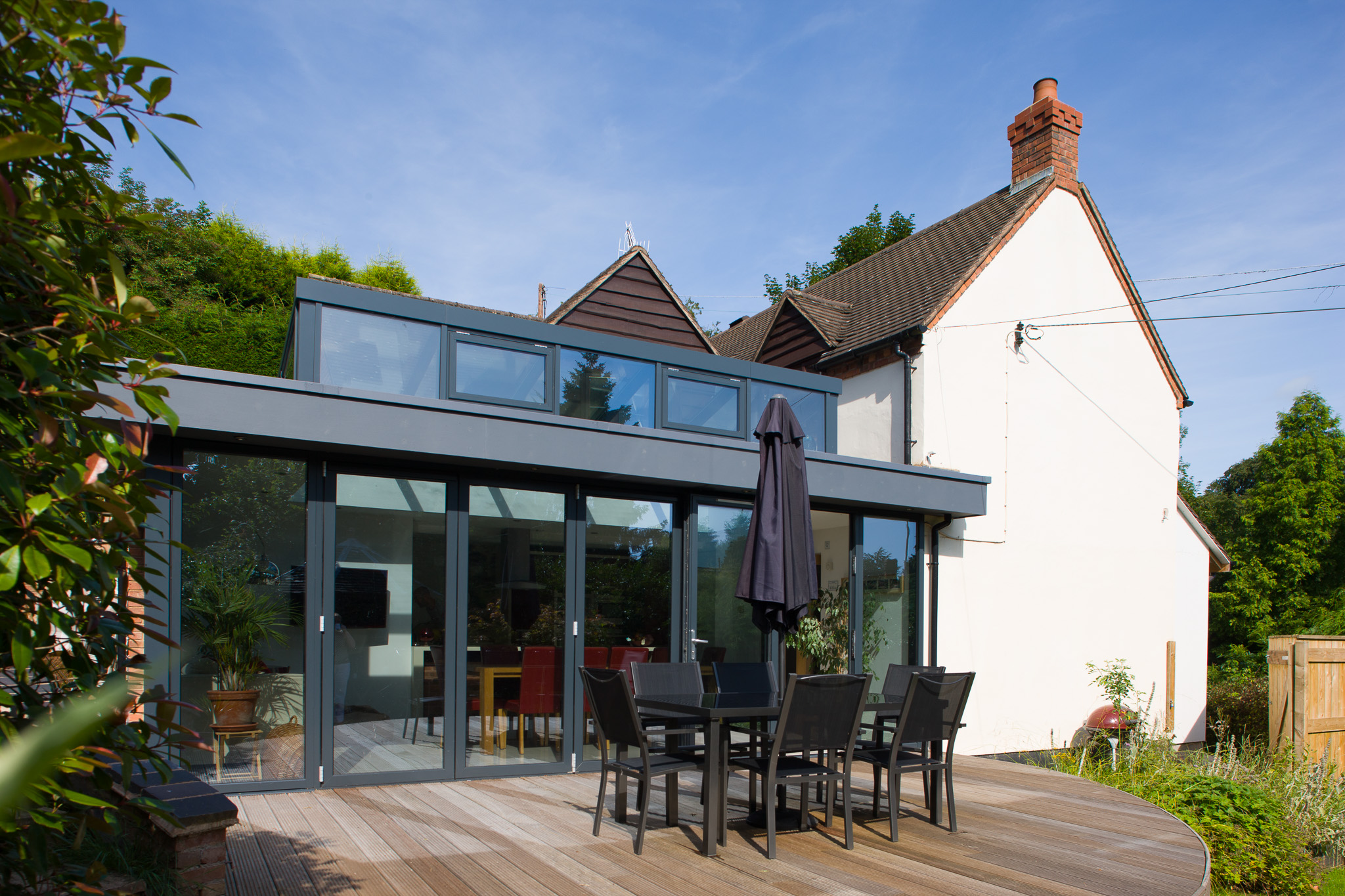
A QUALICOAT licensed applicator, on the other hand, must use a pre-treatment system that is QUALICOAT approved and utilise powder systems that are also approved by QUALICOAT, this ensures quality is maintained through the coating process. Furthermore, QUALICOAT licence holders are randomly inspected twice a year to ensure the QUALICOAT specification is being met. Licensed coaters who fail these third-party inspections, will lose their licence.
So, the best specification for any architectural powder coating project should simply be ‘coated by a QUALICOAT licensed applicator’. Known across the globe, with a global supply chain and local licensed coaters, a QUALICOAT specification can be supplied on any continent.
Powder coat failures fall into two broad categories, that of a complete failure of the coating where it simply peels off and failure called ‘filiform corrosion’. This is where oxidisation forms at the edge of a cut or punched hole in the aluminium and appears under the coating as spider like strands of corrosion. Often this failure is seen several years after installation and indicates poor pre-treatment prior to powder coating.
Other problems with powder coating can include fading of colour, loss of gloss and ‘chalking’ of the surface finish. The first two are generally a normal ageing process and the powder coating should still adhere fully to the aluminium and continue to protect the aluminium. Chalking, is also part of the ageing process and appears as a milky surface or ‘chalk’ on the coated surface. This only forms when the finish is generally neglected and not cleaned down within an agreed cleaning regime. Often chalking can be removed by simply cleaning the finish several times over a period of time. Specifying a QUALICOAT Class 2 powder, which uses more robust compounds in its composition, can significantly reduce these issues.
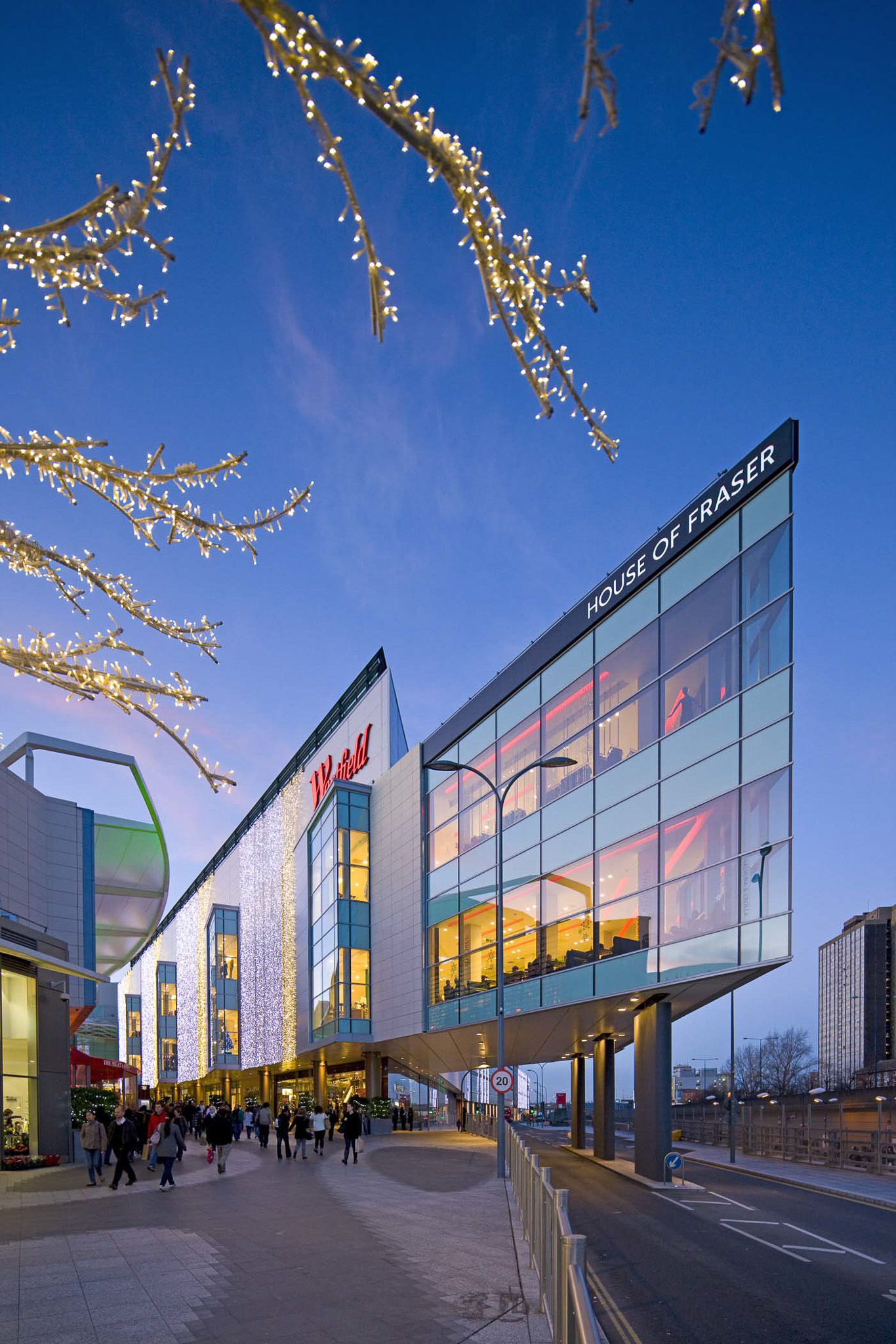
QUALICOAT powder applicators can advise of a suitable cleaning company and there is also a paper on the QUALICOAT UK & Ireland website that explains how the powder coating can be safely cleaned.
For the best sustainability, ensure that the powder coater has the necessary pretreatment systems in place and that they can demonstrate that they can coat and test to BS EN 12206-1. Alternatively, just insist on a specification that powder coating must be applied by a QUALICOAT licensed applicator. In the UK, the majority of main architectural powder coaters are qualified QUALICOAT licence holders. If you are proposing to specify an architectural coater who powder coats to BS EN 12206-1, be vigilant to ensure that they posses a robust pre-treatment plant and that their processes are correctly monitored and maintained.
Should a coating specification require a longer life expectancy, possibly where future access for cleaning be difficult, then a Class 2 more robust powder can be specified. Contact any QUALICOAT licensed powder coat applicator or powder manufacturer to seek advice for any project location across the UK & Ireland.
Various country Members of the global specification, QUALICOAT, have undertaken extensive work over the decades to further refine the products and processes to ensure finishes continue to offer enhanced sustainability. A worldwide working group of Members began to develop a specification for the alloys used in extrusion for fenestration, namely architectural aluminium alloy grades of 6060 and 6063. The resulting alloy specification, which now forms Appendix A13 of the QUALICOAT Specifications 2023, requires these alloys to fall within the EN573-3:2019 Standard, which can be met using primary or secondary (recycled) aluminium. Compliance requires the following three tests to be carried out, Optical Emission Spectroscopy (OES), Anodic Cyclic Polarisation (ACP) and a metallographic study of the aluminium surface. This latest development has culminated in forming what is now known as the ‘QUALICOAT 3.0’ specification.
Specifiers who wish to take advantage of QUALICOAT 3.0 should in the first instance contact QUALICOAT UK & Ireland for guidance on specification and help in choosing the correct supply chain. A QUALICOAT 3.0 specification will require a coating Member to carry the ‘Seaside’ class pre-treatment license as this is a prerequisite coating procedure for QUALICOAT 3.0.
The most important aspect to specification is the involvement of a specialist coater at the early design stages of any project. All QUALICOAT UK & Ireland members are available to offer advice and can be found on the Association website at qualicoatuki.org