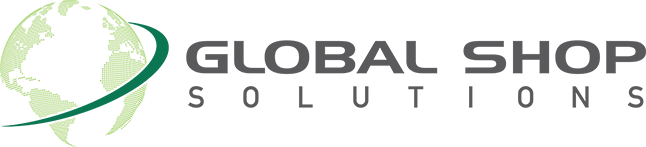
THE WOODLANDS, TX, April 2015 – For most manufacturers, determining how much individual inventory cost components contribute to the total cost of finished goods can be a difficult and uncertain process. Global Shop Solutions, a global provider of enterprise resource planning (ERP) software for discreet manufacturers, takes the mystery out of this process with the introduction of FLOOOM – a new software release that takes a giant step forward in ERP job costing capabilities.
“Too often, individual costing components such as labor and materials get lumped together when determining finished goods costs,” says Dusty Alexander, CEO of Global Shop Solutions. “When cost of goods sold starts to creep up for a product line, it can be very difficult to pinpoint which cost components are causing the increase. FLOOOM measures Freight, Labor, Overhead, Outside, Other and Material so our customers can determine their individual costing components with remarkable precision.”
With FLOOOM, manufacturers can get reliable answers to critical job costing questions such as:
- How much labor and material went into this part?
- How does the cost breakdown compare with past production?
- Which process needs to be improved to lower costs?
- How will a change in production costs (such as material) affect the financial statement?
In addition to identifying the percentage of each cost component for work in progress, FLOOOM also provides powerful historical tracking capabilities, offering an instant time-lapse view from past to present of every part that has passed through the shop floor. Manufacturers can simultaneously view old quantities and cost, current transaction and cost, and new quantity and cost, as well as a complete history of finished goods costs, allowing them to make better management decisions.
“FLOOOM is all about empowering our customers by providing greater visibility of their cost factors,” adds Nick Knight, Director of Consulting & Implementation at Global Shop Solutions. “The more ways they can look at the data, the greater their ability to fine-tune their production processes to improve the bottom line.”
About Global Shop Solutions
Global Shop Solutions, the only provider of One-System ERP Solutions™ designed to streamline operations, has helped thousands of discrete manufacturers increase sales, improve quality and on-time delivery, and lower costs. Global Shop Solutions is headquartered in The Woodlands, Texas, with offices in major cities throughout the United States, Mexico, Singapore, Indonesia, Australia and New Zealand, serving customers in a variety of industries throughout the world. Global Shop Solutions’ unique combination of manufacturing knowledge, software expertise and commitment to customer service has produced more successful implementations than any of its competitors in the industry. For manufacturing companies that want to provide better and faster service to their customers, gain more control over their business and accelerate growth and profitability, Global Shop Solutions is the ERP software of choice.
For more information please visit www.globalshopsolutions.com.