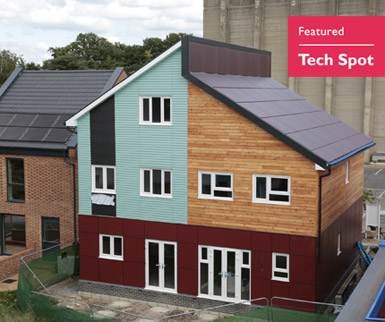
A new housing concept delivers on cost, quality and sustainability and cuts construction time in half
Housing decision-makers across the UK can explore the affordable, energy-efficient, quick to build volumetric housing solutions brought to market by Üserhuus AG and Tigh Grian Ltd at the BRE Innovation Park in Watford.
The world renowned BRE Innovation Park, created in 2005 to trial, test and demonstrate low and zero carbon homes and buildings of the future is now host to two new housing units. These demonstrate the ultimate in super-efficient, factory-finished, configurable dwellings built to the Scottish Building Regulation Gold Standard, with one unit having a completely building-integrated photovoltaic roof.
At the heart of the project is the volumetric unit, comprising a single-bed apartment or a combination of units forming houses of up to four or five bedrooms. Manufactured in Wales using a structural insulated panel system (SIPs), the 4.9m x 11.4m modules can be assembled into units of up to five storeys in detached, terraced, tenement, semi-detached and four-in-a-block configurations giving occupants and housing associations a low-cost, energy-efficient solution without compromising on good design and comfort.
Each unit is built, fully serviced, fitted out and decorated practically ready for occupation upon leaving the factory, when it is transported via lorry to be laid on pre-prepared foundations. With EPC B ratings, each unit is fully insulated and heated using a whole house mechanical heat recovery ventilation system, with wall-mounted electric panel heaters.
With Üserhuus’ input, there is also the option to replace the tiled roof with an entire photovoltaic “terra cotta” roof and part of the façade. The basic house types aim to deliver very low annual energy bills (estimated at £300-500 per annum for energy and space heating); with the addition of Üserhuus’ technology they could even produce supplementary energy.
The overall affordability (cost calculations indicate less than £1000 per sq m), reduction in construction costs and the early delivery of houses for occupation, together with the assured and consistent internal quality, makes for a much more efficient use of development finance and earlier achievement of a revenue stream.
Director of the BRE Innovation Park Dr David Kelly said: “We have a chronic shortage of housing in the UK – we need to deliver 250,000 homes a year to meet market demand – last year we managed 118,000, less than half. We need to find new and better ways to deliver and these homes are a step in the right direction. What is really impressive about the home aside from its affordability and sustainability is that it reduces end to end construction time by half, so eight weeks from factory to completion on site – currently the average home takes a minimum of 16 weeks to build.”
Dr. Stephen Wittkopf, Managing Director, Üserhuus AG, commented: “The future of architectural design lies with the integration of renewable energy technologies. The project on the BRE Innovation Park is showcasing a first-in-the-UK integrated, terracotta style cladding and roofing PV system which points the way for future housing – we are looking forward to seeing how it performs and we want to test other technologies.”
The Üserhuus/Tigh Grian concept has already been commissioned for use on a 50 unit housing development in Alva Scotland, construction is due to start later this year.