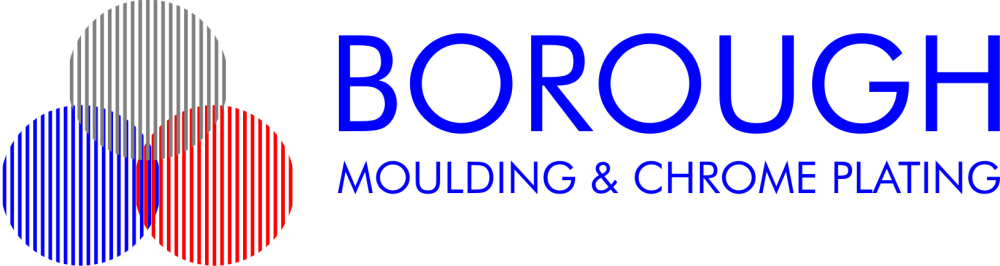
Southend-based Borough Plating, one of the world’s leading chrome-plating specialists, is celebrating 50 years of chrome-plating plastic components, having led the way since developing the innovative process.
At the forefront of the technology here in the UK during the 1960’s, Borough Managing Director David Coombes has witnessed a lot of change in the past 5 decades: “Recent talk of England’s ’66 World Cup win brought back memories of a busy year for Borough.
“It was 1966 when we transitioned from a traditional chrome plater and metal polisher into one of the very few companies capable of successfully chrome-plating plastic components, typically moulded from ABS. We started with radio and television control knobs, with our plating quality attracting work away from vacuum-deposited chrome, which has nowhere near the durability of electroplated chrome.
“The top three selling cars in that year were the Austin 1100, the Ford Cortina and the Mini, all of which used a lot of chrome-plated components. Our business received a significant boost when we supplied chrome-plated plastic lamp surrounds for the Mini, the start of our relationship with the automotive sector.
“The biggest advantage of the process we developed was to offer automotive designers more freedom with plastic components than they typically experienced with die-casting. Chrome was still required for embellishment, but now they could combine this greater design freedom, with the ability to save weight. And as we all know, weight-saving helps performance and fuel economy.
“In those early days we typically plated components supplied by other manufacturers within the automotive supply chain or direct for the car-makers. This was before the concept of Tier 1, 2 and 3 suppliers or entire assemblies being completed off-site became today’s reality.
“In the early days, chrome plated plastic components really only featured inside cars. It took time to create a plating process that delivered the quality and durability needed for exterior trim on some of the biggest marques of the period. As we entered the ‘70’s our chrome-plated plastic grilles graced the fronts of the Jaguar XJS, the Austin’s famous Maxi and Princess.”
Borough has continued to supply high quality chrome-plated components to the automotive industry with interior and exterior trim adding design polish to models by Rolls Royce, Bentley, MINI and Mercedes to name but a few.
To improve the quality of the finished chrome-plated components, Borough helped develop new design techniques for the ABS mouldings to be plated. Borough has since continued to invest in new technology to enhance its own injection moulding capabilities at its Southend production facility.
Coombes continues: “As the demand for high quality chrome plating has increased, from the automotive sector in particular, we recognised the quality of the moulding was the limiting factor. The combination of high quality injection moulding and 50 years’ experience of chrome plating ensures Borough will still be an important member of the supply chain when 2066 arrives.”