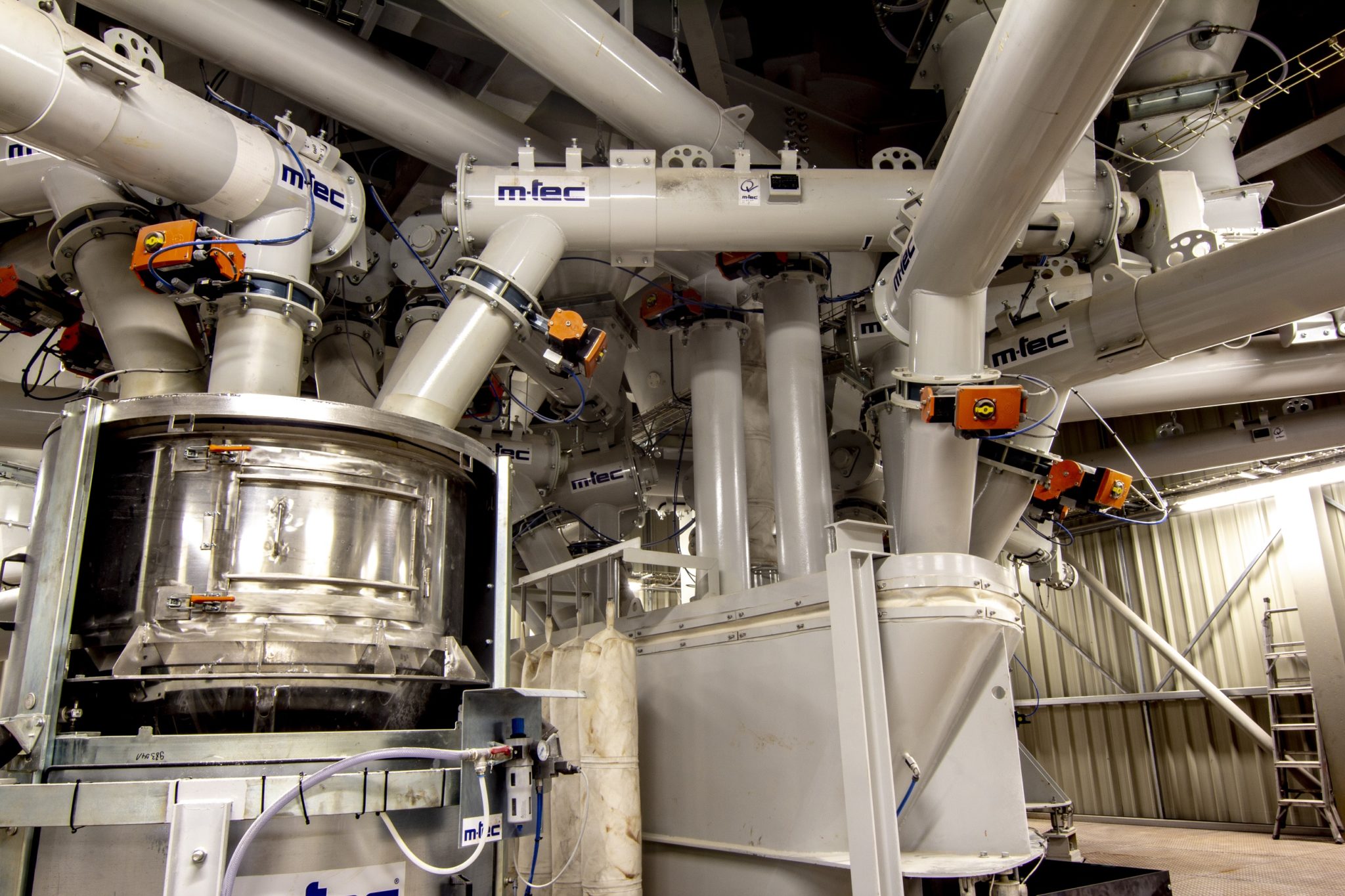
The UK construction industry is shifting to favour healthy materials over their synthetic alternatives and as a result, the use of lime in buildings is seeing a significant revival.
That revival isn’t limited to historic building conservation projects though, we’re starting to think about how our building materials are influencing our well-being, prompting us to make healthier choices.
Architects, specifiers and designers are all beginning to recognise the myriad benefits that lime materials offer to building projects.
But how are lime materials formed? How are they different? Where is it best to use them?
Mortars, renders and plasters
Mortars, renders and plasters are mostly made of sand or aggregate and a binder which holds the materials together.
The importance of sand within any mortar or plaster should not be under-estimated. Sand provides a large proportion of the material’s overall volume and acts to prevent shrinkage as it dries out. It’s a key constituent for strength and durability, as well as the overall aesthetic appearance of the mortar or plaster. Equal time should be spent analysing and choosing the sand within the mortar mix as is spent on the binder that holds it all together.
Binders take many forms. They can be clay, cement, gypsum or more recently, synthetic, petrochemical-based plastics like silicone or acrylic. But for a long time – and increasingly more so as we move to build more healthily – the material of choice was lime.
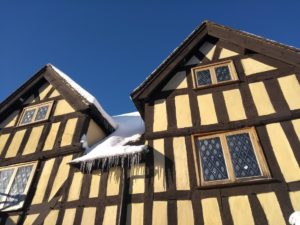
Lime mortars, lime renders and lime plasters
Lime, water and sand are the three primary ingredients in lime mixes. Once mixed, these set to form something similar to man-made limestone.
Although limes might differ across chemistry and strength, they are all made by heating natural limestone in a lime kiln. This produces the highly-caustic unslaked lime or quicklime to which water is then added to produce the slaked lime.
Different limes after this stage set and harden differently.
Non-hydraulic limes (hydrated lime or lime putty) set by absorbing carbon dioxide (CO2) from the atmosphere and hydraulic limes set by reacting with water. Non-hydraulic limes have a much slower setting time than hydraulic limes as exacting conditions need to be met in order to facilitate the absorption of CO2.
Hydraulic limes will even set under water. These are made in the same way as non-hydraulic limes but are burnt from a different limestone. These materials initially set when water is added but then harden over time as they absorb CO2 to give harder, more weather resistant mix.
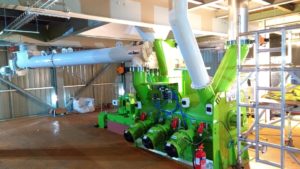
What are the pros and cons of lime materials?
Benefits
Some of the benefits of lime are long-established such as its natural antiseptic properties reducing the risk of mould growth. But there are many more positive aspects to working with lime materials:
- Breathability
Predominately, lime materials offer breathability as they are vapour-permeable. This means they allow water, as a vapour or a liquid, to pass through, avoiding the build-up of trapped moisture and therefore reducing the risk of damp, rot or condensation within a building’s fabric.
- Durability
When used carefully, lime is exceptionally durable[i]. There are many examples which highlight how lime has stood the test of time – such as Rushbury Manor, a 400 year old manor house built using lime materials. As lime works to keep the underlying structure of a building dry, it allows for a more durable and sustainable building structure.
- Workability
Lime has amazing workability, with a sticky, ‘fatty’ feel for the applicator. The workability and ease of use of render, plaster or mortar is really important to achieving the desired aesthetics of the end result[ii].
- Beautiful aesthetics
Lime avoids the synthetic look of many alternative materials, ageing gracefully over time – sometimes looking even better with age. Lime mortars, renders and plasters can also be produced in a wide variety of colours.
Drawbacks
There are, of course, limitations to the use of lime materials and there are some environmental scenarios which make building with lime an unsuitable choice:
- Slower setting
Some lime materials require more methodical planning and working practices as some mixes can take longer to set than synthetic alternatives.
- Confusing terminology
Sometimes, it can be unclear exactly what’s contained within so-called ‘lime’ products, particularly when dealing with imports. It’s important to take care when buying to ensure you’re not paying extra for what is nothing more than white cement.
- Fear of use
Builders are sometimes wary of switching to lime products – dismissing it as ‘too difficult’ or ‘too slow’. Lime materials aren’t necessarily more difficult to use than others, they’re simply different. It’s more straightforward than you might think.
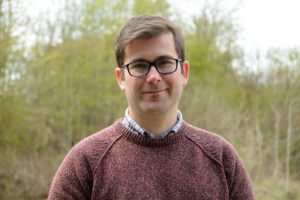
Top tips for applying lime
- First decide which style and finish you want
That will ensure you have the right product for your beautiful project result.
- Ensure you select the right product for your project
Is it hydraulic or non-hydraulic lime? How hard is the material you’re using? How exposed will the material be to the weather? This may help https://www.lime-green.co.uk/knowledgebase/hydraulic_or_hydrated_lime.
- Add water carefully
Water is only needed for hydration to make the lime mix spreadable, sticky and workable.
To understand more about how lime may suit your project or to explore our range of lime products, visit www.lime-green.co.uk or call 01952 728 611.