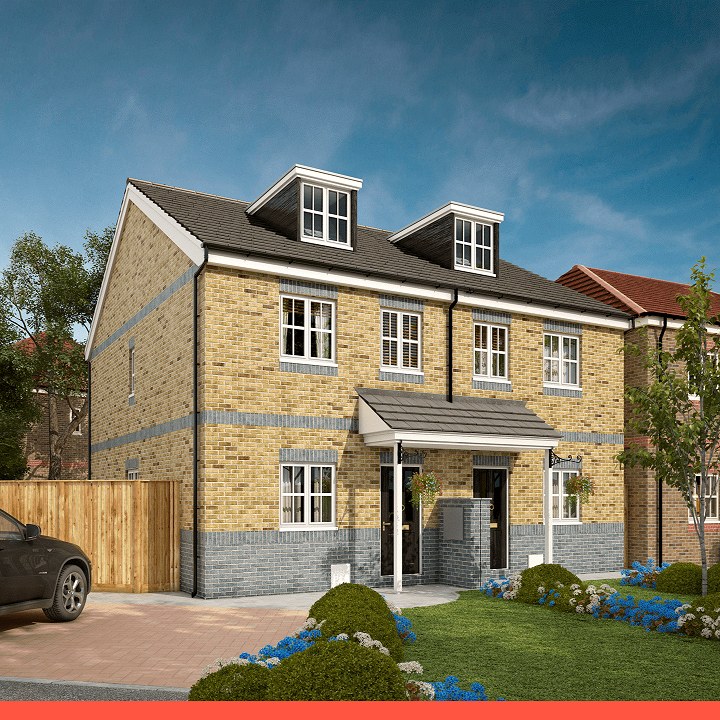
IT’S no secret that the UK is suffering from a housing crisis. Modular homes are seen as the answer. Modular homes are designed to be incredibly energy efficient – some costing just £1 per day to run – and efficient to manufacture – with some developments boasting a one-week onsite build time. What’s not to get excited about?
But it’s not just architects and contractors who are having all the fun in developing this new approach to housing. Engineers are also challenging the norm when it comes to creating eco-friendly and efficient-to-erect homes.
“Compared to the design of standard residential homes, modular homes are a completely different product and require a wholly new approach,” said Wayne Oakes, director at civil and structural engineering practice, Dice.
“During our first modular project we spent a considerable amount of time liaising directly with the manufacturer regarding specific details and design standards – most notably with regards to National House Building Council (NHBC) requirements for the substructure. This was a requirement of offsite manufacturing partner ilke Homes’ properties, to ensure that each of the plots met the requirements of building control.
“Since then, we’ve learnt a lot. Perhaps the biggest challenge we have faced to date is attempting to retrofit a brownfield site on behalf of a developer who purchased the site, prior to fully understanding the constraints and nuances associated with the product.
“Modular units have specific requirements in terms of their sub-structures and external works designs – particularly in the case of sites with gradients and surface water management requirements, which would not be considered ‘the norm’ for standard residential units.”
Dave Sheridan, executive chairman of specialist housing manufacturer ilke Homes added: “Offsite modular manufacturing’s time has finally come. The traditional construction industry is in desperate need for modernisation and we must do everything we can to pull it into the 21st century.
“Modular can be the pole that brings balance back to the industry, creating new homes, new jobs and new investment opportunities
“With greater collaboration between government bodies, housing associations and private companies, house building in the UK can get the jolt of energy it needs to ramp up supply and deliver high-quality homes to everyone. Whether they’re a first-time buyer or a family needing social housing, the pace at which we can deliver offsite manufactured homes means that housing shortages could become a thing of the past.”
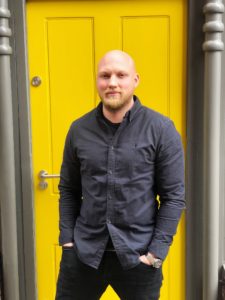
Although modular homes are a relatively new product, technology is quickly making the process easier. But in an industry that’s traditionally been seen as slow to adapt – can construction keep up?
Wayne continued: “In short: yes. Undoubtedly the technology is already here – and more is developing every day. In the past, there have been question marks over the build quality and durability of modular type systems. However, with increased product innovation also comes greater flexibility and some of the products now available on the market are fantastic.
“As engineers, we’ve certainly realised technology’s potential. Whereas we were once seen as reluctant to change – we’re now driving it, thinking creatively to develop new concepts of living.
“It all comes down to time saving. Offsite construction enables phases of work to be undertaken concurrently. Onsite substructure and infrastructure work can be taking place whilst the superstructure is being built in a factory. Factory conditions also mean that there are no delays due to inclement weather – a common issue in the UK.”
The efficiencies relating to modular housing are now catching the attention of big businesses.
Places for People has recently pledged £100 million – the biggest investment in modular by a housing association to date – to acquire 750 new units from ilke Homes.
Homes England has also announced that it will be delivering 400 modular homes by regeneration specialist Urban Splash, alongside the Japanese modular specialist Sekisui.
Even the likes of Goldman Sachs is getting involved, investing £75 million into TopHat’s modular housing product.
“Big businesses are seeing the investment potential in modular homes – which is a huge vote of confidence for the industry and will mean big things for the future of the sector,” added Wayne.
“But we’re particularly proud to have also worked with small, eco-focussed and private developers – as well as multi-national housebuilders.”
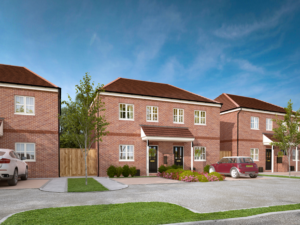
Dice recently worked with developer Positive Homes, which prides itself on creating houses which cost just £1 per day to run. Martin Valentine, managing director of Positive Homes said: “Our bespoke development in the heart of Nottinghamshire will see the creation of nine new properties – which require a four-day onsite build time.
“We anticipate that these homes will be sold off-plan due to the high-quality finish, unique design and environmentally-friendly aspects – without the ‘eco-premium’ price tag. These really are the real benefits of modular housing.”
Wayne continued: “Where engineering can benefit is through working closely with the manufacturer to ensure that the groundworks packages are fully coordinated with the modular units before they arrive onsite.
“Our remit has focussed on sub-structures – designing a foundation that is fully co-ordinated with the offsite manufactures superstructure and service locations – and the development of the associated civil and infrastructure – designing roads and drainage to cater for developments which can range from nine bespoke units to hundreds of affordable, standardised properties.
“Engineers need to be agile, responsive and willing to adapt to clients’ modular requirements, responding to site specific requirements and being bold when it comes to challenging a design.
“Yes, modern methods of construction have perhaps been slow to get off the ground. But now that the right people have bought into these principles, I think we’ll be seeing a flurry of projects which incorporate these low carbon, offsite build methods.
“We’re a relatively new business – opening in 2018 – but we’ve already completed 100 modular units and are now the recommended engineer for ilke Homes. This is a sign of things to come. The future is very much modular.”